During the early part of 1979, Ruston Diesels Limited, the Company then occupying the historic Vulcan Foundry site, agreed to restore the locomotive Lion which had been a static exhibit for many years in the Transport Gallery of Liverpool Museum. This was to provide project work for apprentices and graduate trainees, and to enable Lion to participate in the forth-coming ‘Rocket 150’ celebrations. On 4 April, the engine arrived at Ruston’s looking rather incongruous on the back of an articulated lorry and during the next few weeks it was stripped of its oak boiler cladding, brass firebox dome, splash guards and other embellishments. With the basic structure once again jn view. Lion was subjected to various examinations to measure and catalogue its many parts and to assess the viability of the project.

For readers unfamiliar with Lion’s history, it was built in 1838 by Todd, Kitson and Laird of Leeds, the pre-decessors of the later firm of locomotive builders, Kitson & Co Ltd. Lion saw some seven years of service on the Liverpool & Manchester Railway as No 57, and 14 years on the Grand Junction Railway and London & North Western Railway as No 116. In an era of rapid locomotive development, it was considered obsolete by 1859 and was sold to the Mersey Docks and Harbour Board for use as a stationary pumping engine at the Princes Graving Dock. Lion was rescued from
obscurity in 1928 and was subsequently restored by the LMS at Crewe for the centenary of the L&MR (see January 1980 Railway World), when it ran on a special track at Wavertree, Liverpool.
Afterwards, Lion was exhibited on a plinth at Liverpool Lime Street station, being taken to Crewe for storage during the war, and making brief excursions to appear in films. Indeed, Lion’s last public steaming was in 1952 as the star of the Ealing comedy, The Titfield Thunderbolt. To ensure its preservation, it was eventually placed in Liverpool Museum’s Transport Gallery in 1969.
Lion is now ostensibly 142 years of age and claims the record as the world’s oldest original operating locomotive. However, to maintain this title, many of Lion’s components have been replaced over the years and it is questionable just how much of the original locomotive remains. The classical chimney, the oak cladding, the footplate balustrades and the firebox brass dome all date from the 1929 reconstruction by the LMS. The dome in fact is most misleading and gives the impression that Lion has a ‘haystack’ firebox crown. However, when this brass ornament is removed, it exposes a Stephenson ‘vaulted arch’ type of crown which is topped by a cylindrical, flat- topped steam dome. The origin of the tender is somewhat obscure. It is apparently a relic from the Furness Railway which the LMS modified to suit Lion. Although it gives the impression of an 1840s’ tender and is convincingly corroded on some of its upper plates, the axleboxes, fresh timbers and arc welds indicate its more recent construction.
Returning to the engine itself, what of the boiler, frames and motion? According to Whishaw’s contemporary publication Railways of Great Britain and Ireland 1842, Lion was delivered with an oval boiler which measured vertically 42in, transversely 39in and was 89in long. The boiler tubes were l5/8in in diameter and numbered 126. It is interesting to note that this early experimentation with oval boilers resulted from the misconception that a locomotive’s centre of gravity had to be kept as low as possible. Lion’s boiler today is circular with a diameter of 40in, a length of 104in and with 98 tubes of 2in diameter. According to the Catalogue of British Locomotives Vol 2A (Moorland Publishing), Lion was re-boilered during 1844/45 and the cylinder diameter increased to Min. It is doubtful if the present boiler dates from 1844, but it is perhaps safe to assume that it is of the same design. A brass number casting, ‘149’, is screwed to the boiler just above the regulator and the wrapper plate is stamped ‘RN 149’ and ‘REP.D TEST 70LB 20.6.02 W.E. M.S.U.A.’. Even with these clues, the origin of the present Low Moor iron boiler has not been discovered.
Lion’s frames are undoubtedly original although the horn plates show signs of repair. The outer frames have a sandwich construction as patented by Stephenson 246 and comprise a wooden beam faced with through bolted wrought-iron plates. At either end of the locomotive, these are tied together by the huge baulks of timber which act as buffer beams. The corner joints appeared to rely only on angle-iron brackets and during the restoration it was something of a surprise to find that the timber-work was also connected with mortice and tenon joints. Sadly, both buffer-beams are now badly cracked. The LMS reinforced the rear beam with a length of channel section and a similar measure has now had to be taken at the front. The buffers themselves are made from iron hoops and leather, relying on horsehair for their resilience, and are built around iron plungers which slide in the buffer-beams. Again, these are reconstructions by the LMS.
The inner frames are made entirely of wrought-iron and are interestingly shaped and sculptured. While these extend from the smokebox to the firebox, they only carry bearings and inner springs for the cranked axle. When Lion was in service as a stationary engine, the trailing axle was removed and the rearmost legs of the associated hornplates were cut away to allow tressle mounting. These were repaired by the LMS as the unpitted plating testifies. Of more interest, however, are the crank axle hornplates. On the right- hand outer frame these are attached by 10 bolts in a double five domino pattern. On the left-hand side there are only eight bolts in a double four configuration. There could be many reasons for this difference. One suggestion is that the extra two bolts were inserted when, following a crankshaft failure on the tight Newton-le-Willows curves, a new hornplate was fitted. The fact that the locomotive has had a new crankshaft would seem indisputable. Wishaw quotes Lion’s original piston stroke as 20in while today it is only 18in.
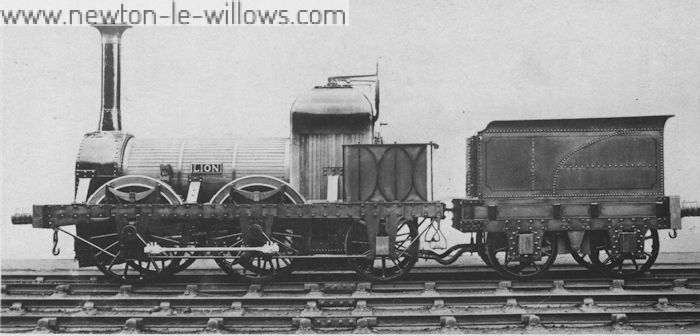
Why this change was made may never be known. It could well have been occasioned by a crankshaft failure, with the engineer of the day attempting to obtain a stiffer component with the replacement shaft. But it is more likely that with the larger replacement boiler, a smaller crank throw was required to obtain the necessary running clearances. This would have obviously resulted in a loss of tractive effort had not the cylinder bores been increased from 11 in to 12in and eventually to Min.
Considering Lion’s motion in detail, the cylinders are placed low down in the smokebox and are inclined at 4| degrees so that the piston rods pass below the leading axle. The crosshead slides are located at the front by tapered studs into the cylinder covers, and are carried at the rear by a pair of‘spectacle’ frames through which the connecting rods pass on their way to the crank axle.
From each of the two crossheads, plunger-type boiler priming pumps are directly driven, the rate of water feed being controlled by the valves on the tender. The 5ft diameter driving wheels have 18 spokes and carry tyres both shrunk and bolted to the rim. The wheels on the leading axle are similar but only have 16 spokes. Each wheel is inscribed ‘Rothwells Bolton’ and probably date from a major overhaul. The tyres are now very worn, and although passed by the BR inspectorate for running at Rainhill, they will need reprofiling if Lion is to steam many more miles. It was most
fortunate that the locomotive’s trailing axle, though discarded on a nearby scrap- heap by the Harbour Board, was not actually destroyed, but the corrosion on the wheel spokes testifies to many years of exposure to the elements.
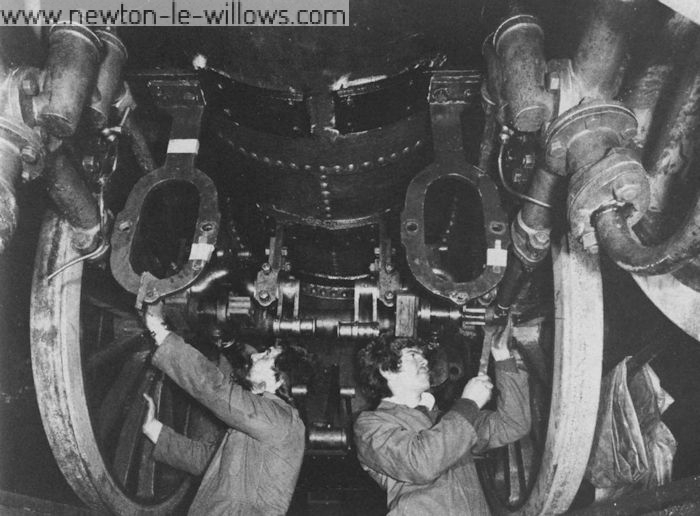
Perhaps the most interesting feature of Lion is its valve gear, commonly referred to as ‘gab’ motion. The valve chests are located on top of the cylinders and the valves themselves (still relatively unworn) are driven by rocking levers, the upper ends of which are connected to the valve spindles while their lower ends carry rollers with which the eccentric rods engage. For each cylinder there is a fixed eccentric and rod for each direction of motion which results in four units. The eccentric rods terminate in wide-mouthed forks or gabs. When engagement is required, the gabs are forced on to the rollers which, in centralising themselves in the ‘vee\ position the valves correctly for the direction required. Lion has a single lever to accomplish this. Moving this backwards lowers the upper eccentric rods on to the rollers and forward ‘gear’ is obtained. With the lever fully forwards, the lower rods are raised and reverse is selected. As was discovered during the steam trials, it is quite easy to select the gear opposite to the direction of travel while travelling at quite a speed (which is just as well considering Lion has brakes on the tender only!) However, with the engine stationary, should the operator open the regulator before engaging the motion and thus put steam pressure behind the valves, a very strong arm indeed would then be required to select the appropriate gear.
Discovering Lion’s history, technical details, and assessing its condition to lay the foundations for the restoration ahead proved very time-consuming and it was not until late August 1979 that work began in earnest on the locomotive. Its mechanics were basically in good condition, thanks largely to the extensive rebuild by the LMS. However, the years as a static exhibit had taken their toll and many minor items such as nuts, bolts, keys and split pins were damaged, loose, or missing. Many mating parts were incorrectly assembled, some castings were cracked and the gaskets, seals and packings were perished.
While the complete mechanical dismantling was in progress, a crack in the left-hand driving wheel rim (which had propagated from a disused tyre bolt hole) was repaired by the Metalock metal stitching process. This involved dumb-bell- shaped keys being sunk into the metal across the line of the crack, and then screwed studs sheared off in the crack itself to expand the casting on to the keys. It is a particularly effective repair for rim cracks as it tends to increase the compression between the wheel and the tyre.
During these early stages the main concern was with the condition of the boiler, and on 4 September 1979 the first official examination was made by the British Rail Inspectorate. After an hour of ear-splitting hammering on the external plating, and contorted attempts to view the internal condition through the steam dome, the verdict was that while the boiler appeared serviceable, the regulator, main steam pipe, and boiler tubes would have to be removed to allow an internal inspection of the shell plates. This was in line with BR’s policy of a re-tube every ten years for a preserved engine, and to some extent highlights the difference between private and BR operating requirements. For the former, a hydraulic test to twice the working pressure would have been sufficient for the necessary clearance by the insurance companies.
In an attempt to reduce the boiler work, and to minimise the chance of irreparable damage being caused, non destructive test techniques were initially considered. The plan was to isolate each and every boiler tube and hydraulically test these internally to 1,000 lbf/in2, and to use ultrasonic equipment on the shell plates. However, as mentioned earlier, Lion’s boiler is fabricated from Low Moor iron and some research showed that with age this material seemed to ‘segregate’ rather than rust. As this would have led to false thickness readings, the only reliable course of action was to remove the tubes and inspect internally.
The first tube removed from the boiler was cut out using a hammer and a ‘fishback’ chisel. Inexperience, and the extreme care required to avoid tubeplate damage, meant that- this operation took about four hours. Eventually, to speed the process oxy-acetylene cutting equipment was used which in many ways was safer by precluding damage to the copper tubeplate in the firebox, and injury to hands from stray hammer blows. Care and skill was required when cutting against the iron tubeplate in the smokebox although it was found that the relatively thin 12-gauge boiler tubes could be burnt away before the tubeplate itself became hot.
While this job was being carried out, work began on the main steam pipe and regulator, two components which proved particularly difficult to remove. Made from arsenitic copper the steampipe had a 1in wall thickness, was 5in in diameter and some 12ft long. It was attached to the smokebox tubeplate by a large bolted flange, and to the regulator inside the boiler above the crown plate, by four ‘hook’ bolts around a smaller flange. The nuts holding the tubeplate flange were easily undone with the assistance of some penetrating oil, but the corroded hook bolts were extremely difficult to reach and required an apprentice to work literally standing on his head inside the steam dome. In theory, with these bolts removed it should have been possible to slide the steam pipe out of the boiler via the smokebox, but despite considerable effort it remained immovable. In the end, the pipe had to be cut away at the front flange and the flange was removed with a powerful extractor. As a temporary measure Lion is now fitted with a steel steam pipe until the copper original has been repaired.
The sliding plug-type regulator, a brass casting of some considerable weight, was held in place by six double-ended bolts which passed through the back wrapper plate and located the throttle assembly. Each of these large bolts sheared off when an attempt was made to undo them which was rather worrying when the regulator still remained firmly in position. However, after the judicious use of a small hydraulic jack, the seal against the wrapper plate was broken and the regulator hoisted out through the steam dome. It was now possible for a slim person to squeeze into the boiler shell, the space between the vertical stays holding the girdered crown plate being just sufficient.
One of the dirtiest jobs in existence must be descaling the inside of a locomotive’s boiler. Approximately six bucketfuls of rust, scale and cement-like deposits were removed from Lion’s innards by the laborious use of chipping hammers and an air-powered needle gun. The wastage of boiler plates was to a maximum of ‘/gin and this only occurred in a very localised area at the bottom of the front tubeplate. After a week’s hard work, the locomotive was once more ready for inspection by British Rail and the report was awaited with bated breath.
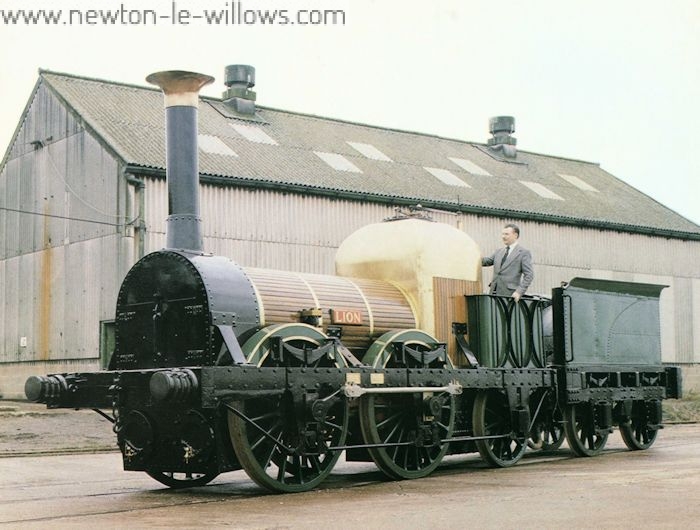
Lion’s boiler showed signs of having been re-tubed many times in the past. The holes in the front tubeplate were sur¬rounded by metal ridges, while each hole in the firebox tubeplate was lined with a thin copper ferrule. After replacing some of these, and grinding the front tubeplate ridges away, retubing began using ‘waterside’ expanding tools kindly loaned by BR. Lion’s tubeplates were found to be bowed outwards by an inch at their centres and each new tube was individually cut to length to maintain an even appearance over the front tubeplate. In the smokebox the tubes protruded y„in while in the firebox the protrusion was 5/j6in. This latter dimension is, of course, quite critical to ensure the correct bending allowance for the tube end beading process.
With re-tubing well in hand, the cleaned engine motion was inspected and reassembled ensuring that the correct running clearances were obtained. As would be expected, considering Lion’s almost negligible mileage since her Crewe rebuild, the bearings and journals were in reasonable condition. Even so, the big-end brasses required closing together and reboring to reduce the 60 ‘thou’ clearance to a more reasonable 10 thousanths of an inch. The locomotive is covered with identification marks which bear witness to many previous rebuilds. It is believed that the original manufacturers used a letter and number code and that the centre punch marks are examples of more recent bad practice. The assembly task was not helped by the fact that many of the markings were contradictory.
Some of the nuts and bolts on Lion were most interesting. Stamped with individual identification marks for both the nut and the bolt, a close examination showed that they were made by upsetting the end of a piece of round bar and then hand filing the hexagon head. Flats turned out to be all lengths, and one bolt in particular required three sizes of spanner for each pair of flats to be used. During assembly, torque set¬tings were obtained from standard tabulated data according to the thread size. Unfortunately, many of the bolts sheared along old fatigue crack lines well before an acceptable torque was reached, but when this happened a marvellous bright silver crystalline structure could sometimes be seen in the metal, probably due to quenching after the upsetting process. Another component found to be extensively cracked was the plunger valve body in the regulator. As this was beyond repair a new component was manufactured from a gunmetal casting.
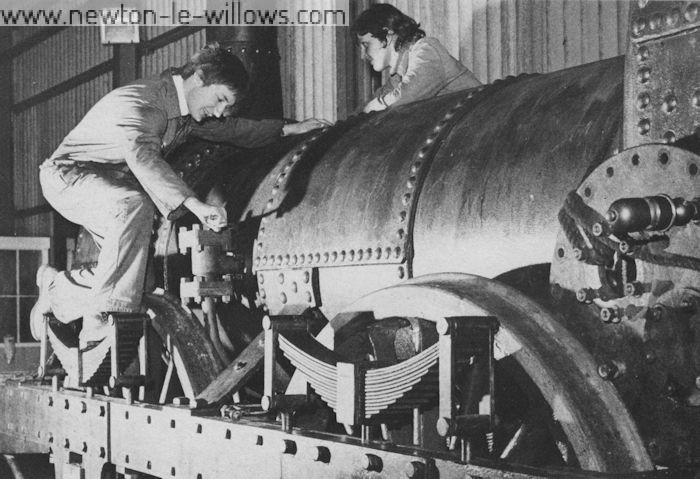
By the time the drain cocks, clack valves and regulator valve were lapped in, the boiler was ready for its first hydraulic test. Water is an amazing fluid. A few tea leaves will often block a sink completely yet leaks will occur past any amount of ptfe tape and thread sealing compound. At least it always seems that way! In fact, the leaks were few and were confined to two or three under expanded tubes and a clack valve gasket. On 11 December we could demonstrate to BR that Lion would hold 100 lbf/in2 in its boiler for a considerable period. A slight seepage occurred from some of the firebox stays and the tubeplate seams, but these were negligible and indeed ceased after the first firing.
The successful completion of the hydraulic tests greatly motivated the workforce and Lion was quickly prepared for steaming, the fitting of the Salter spring balance safety valves and a water level sight-glass taking only a few days. On 13 December (surely this demonstrates confidence!) a warming fire was lit in Lion’s firebox and the following day steam was gradually raised over a period of some five hours until the pressure reached 40 lbf/in2. At 11.03, and in front of local TV cameras, the throttle was opened and for the first time in 27 years Lion moved under its own power.
BR subsequently witnessed steam and motion tests which the locomotive successfully passed. However, on re-examining the cold boiler, twelve firebox stays were found to be suspect and had to be replaced. An excellent technique when visually examining firebox stays through the foundation ring mud holes is to discard electric lighting and to use a flaming torch well soaked in paraffin. The effect is akin to that of a vertical fluorescent tube light inside the water space and gives exactly the right illumination.
During further steam and motion trials, Lion was examined by the Department of Transport Railway Inspectorate who were somewhat concerned by the locomotive’s braking system which amounted to little more than a screw-operated wooden shoe brake on the tender. Although prepared to allow Lion to run at Rainhill as a light engine, its participation in other events and in the haulage of carriages would not be allowed unless certain modifications were made. So Lion’s tender is now fitted with a Westinghouse spring brake system (air off/ spring on) which is compatible with the
replica rolling stock that will appear at Rainhill. No compressor is fitted. Instead, reservoir tanks hidden well inside the tender chassis carry sufficient air for 10-12 applications. This is considered sufficient remembering that the system is for emergency use only. The tanks are charged to 150 lbf/in2 from a portable trackside compressor. Other minor modifications required were the fitting of water level test cocks in case of damage to the sight glass, the provision of safety chains between the engine and tender, and reinforcement of the front buffer-beam.
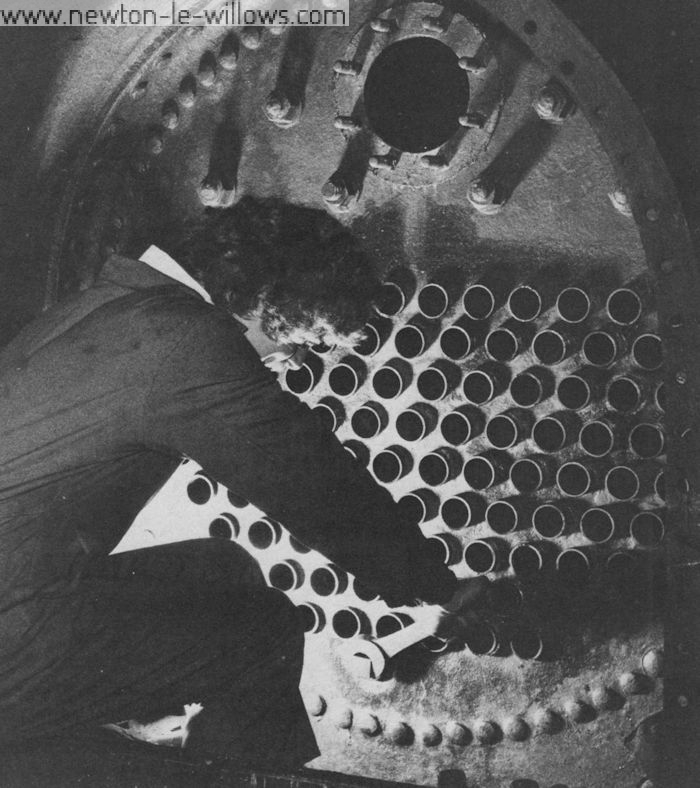
The Lion Locomotive on show at earlier commemorative events.
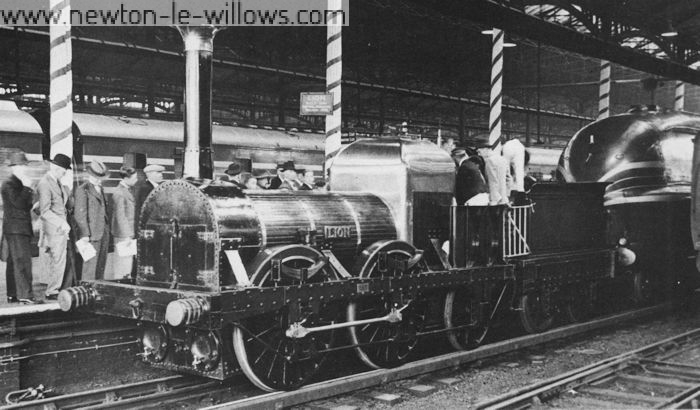
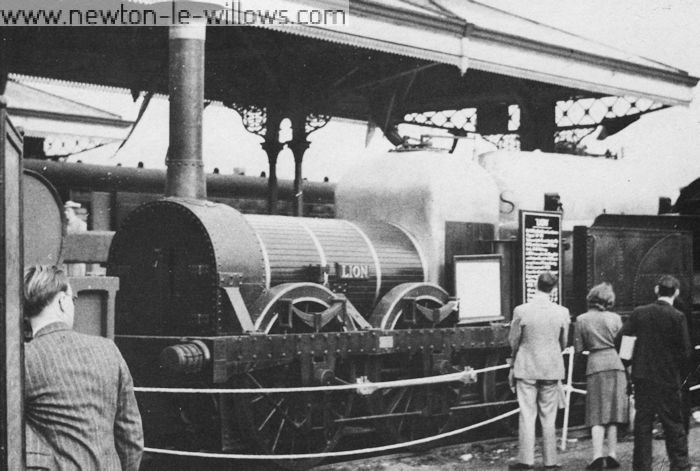
Lion is very easy to operate which is primarily a result of its simplicity, having a lever for the direction of travel and a throttle only. However, a certain skill is required to manage the fire and boiler feed rate correctly. From a cold start the absence of an auxiliary blast to draw the fire is noticeable. This extends the time to raise steam to some 3-j hours, and moreover, when under way for the first time, the previously undrawn fire bursts into life causing the safety valves to blow off for some minutes. When working hard (rolling stock of 20 tons weight has been hauled around the Vulcan site) it is equally easy to run out of steam. Lion will hardly move with pressures below 30 lbf/in2 and blows off at 48 lbf/in2 which is quite a narrow operating margin. To improve the fire control an ashpan damper plate has been inconspicuously fitted. As the locomotive has no injectors or hand pumps, a careful eye must be kept on the water level, for boiler priming can only occur when the engine moves. To run out of steam with a low water level would be most undesirable! Lion rides very smoothly and picks up its heels quickly when running light. In fine weather the wheels cannot be spun which confirms some simple calculations which show its tractive effort to be 3,325lbf and its adhe sive power to be 3,600lbf. It has also been calculated that its maximum load would be around 115 tons. In his book The development of the British steam locomotive E. L. Ahrons gives the average load hauled by Liverpool and Manchester Railway locomotives as
110 tons, so the figure would seem correct. Based on a piston speed of 900 ft/min, Lion’s maximum speed is estimtated as 45mph. However, to assist its preservation for posterity BR has imposed a speed restriction of 20mph. Obviously no speedometer is fitted, but the driver can easily gauge the speed by timing the readily visible outside connecting rods (approximately two revs/sec for 20mph.)
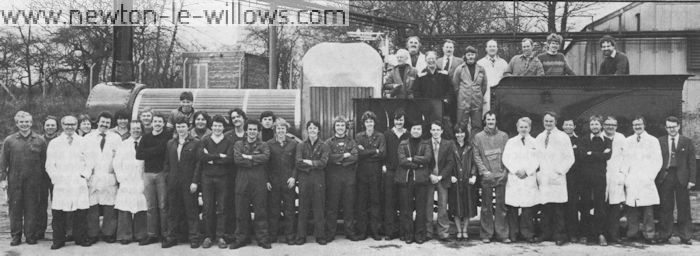
There is little more to add. Lion is once again adorned with its brass dome and wooden cladding (with glass fibre lagging underneath) and has received a new coat of paint and varnish in its L&MR livery. The engine was present at the 100th anniversary of the L&MR and will appear at the 150th. Will she be there at the 200th? To conclude, the author would like to thank all involved with the ‘Lion Project’, particularly the British Rail Inspectors for so generously imparting their knowledge and expertise, and Mr C. E. Taylor-Nobbs for his assistance with historical matters. A final thank-you must go to Ruston Diesels Ltd who so generously provided the author with an engineer’s dream — carte blanche authority and a blank cheque — well, almost!
Mr Morris was the engineer in charge of the Lion renovation project at Ruston Diesels Ltd, Newton-le-Willows.